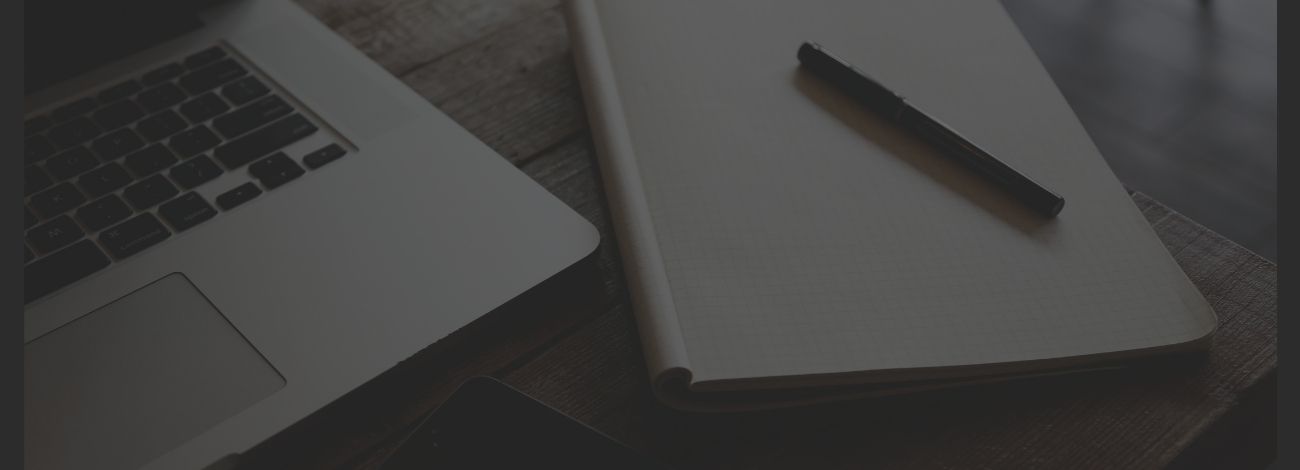
The use of UV curing resins is increasing in high performance products such as films
and smartphones. The reason is that in the process of assembling electronic devices and
laminating of high-performance films, resin is cured by irradiating light for a short time
(only a few seconds) without heating; this makes it extremely effective in mass production
lines of micro and thin film products.
However, adhesion failure is one of the causes of defective products in the
manufacturing process. Although there are various other factors such as insufficient light
intensity, insufficient integrated light quantity, and oxygen inhibition of resin, there are
cases where products’ resin performance do not reach the required standard. In order to
monitor the occurrence of these defects, a sampling inspection method is applied. A random
product is taken out from a certain production line, and then disassembled to check whether
its performance meets standard or not. This method is based on random chance, and does
not allow inspection of all products or guarantee the quality of all others. Moreover, it is also
ineffective and expensive since it ruins the products from the production. For example: in
the manufacturing process of 1,000,000 smartphones – if one in every 1000 devices is
inspected, 1000 devices are destroyed by this sampling method, wasting the product,
interrupting the production line, and causing inefficiency. Therefore, a non-contact,
non-destructive, real-time inspection method to verify the curing of resin is essential.
In this document, a method for determining the curing degree of photocurable resins by
fluorescence is described.
The Curea is a patented fluorescence measurement
device developed AcroEdge. Shown in Figure 1,
this device consists of a sensor and controller,
enabling determination of the curing degree of
photocurable resin in real time.
In principle, a resin as an object to be measured
is irradiated with a weak ultraviolet light source from the sensor. It receives the energy then
emits light back to the sensor, and thus the curing level is determined by measuring the
amount of this emitted light.
FT-IR measurement techniques have long been used as a way to estimate the
degree of polymerization undergone by a UV curable resin. For example, in the
curing reaction process of a radical polymerizable UV curable resin, unsaturated
C=C bonds in the monomers and oligomers undergo a chain reaction caused by the
free radicals generated from a photopolymerization initiator. In this process, the
bond absorption of C=C reduced. The stretching vibration band of a C=C vinyl
group is observed at 1640 to 1620 cm-1, and so the degree of polymerization can be
estimated from the decrease in the area of this peak.
However, typical UV curing resins are a mixture of different resin components,
and often have unsaturated bonds such as benzene rings in the resin skeleton. Since
the absorption peaks of unsaturated bonds have aborbers in similar regions, they
often overlap with unsaturated bond peaks, and thus make it difficult to accurately
measure the curing rate and degree this way.
When an aromatic or similar compound absorbs energy from light, it enters a
state of high energy. This is called an excited state, and the low-energy state prior to
energy absorption is called the ground state. Compounds in excited states tend to be
unstable, and so the extra energy is released for the molecule to return to the stable
ground state afterwards. Typically, there are three ways to release this energy:
1. Use of energy to cause a chemical reaction and form the ground state
of another compound
2. Release of energy as heat
3. Emission of energy as light
The UV curing resin undergoes the scenario detailed in #1, in which the
absorption of UV light causes a polymerization reaction that cures the material.
This reaction is started by a photopolymerization initiator in the resin that has:
1. High ability to generate active species (radicals and acids) for
initiating polymerization reaction
2. Ability to generate highly reactive active species
3. Excitation energy to initiate active species generation in the
ultraviolet region.
When the photopolymerization initiator (or photoinitiator) absorbs UV light, it
produces reactive species either by photodissociating into two split molecules, or by
energizing electrons sufficiently to transfer to other molecules. From here, the
reactive species then form bonds that are the ends of polymer chains. We have
found that molecules attached to these ends emit fluorescence. That is, the emitted
fluorescence intensity is considerably proportional to the extent of the
polymerization reaction (degree of cure) of the ultraviolet curing resin.
Therefore, the degree of curing of the ultraviolet curing resin can be estimated
based on the amount of change in fluorescence intensity before and after the
reaction. For a resin undergoing UV curing, the fluidity decreases as the reaction
proceeds. The viscosity changes in the local environment around the fluorescent
substances significantly influence the fluorescence intensity. As local viscosity
increases, fluorescence quenching caused by local vibrations is suppressed,
resulting in an increase of fluorescence intensity. In the case of a UV curing resin, it
can be said that the main cause of the increase in fluorescence intensity is the
decrease in mobility due to the polymerization accompanied by crosslinking and the
local change in temperature.
Since the polymerization initiator is a main factor of fluorescence, obviously, the
amount of luminescent fluorescence varies depending on the type of the initiator. In
the case of the same initiator, the correlation between the emission curve and the
degree of curing gives consistent data. Fig. 3 shows an example of the temporal
change of the fluorescence intensity. As the curing of the resin proceeds, the
fluorescence emission increases, but as the polymerization rate progresses, internal
stress is generated due to increasing viscosity and decreasing fluidity of the material.
In this case, a part of the light emission energy by fluorescence is temporarily
converted to internal stress energy, and the fluorescence decreases. However, as the
internal stress is relaxed with the passage of time, an increase in fluorescence is
observed again. Until this was known, there has been no method for directly
observing the relaxation of the internal stress of the resin; now, it has become
possible via the continuous measurements of a fluorescence sensor.
Copyright © 株式会社アクロエッジ All rights reserved.